As part of a wide-ranging retrofit and extension of an old farmhouse in rural Northamptonshire, Beautiful Basements was asked to provide waterproofing design, complete build, and waterproofing installation. The project included a new basement under the main house and an extension into the gardens with a basement under that.
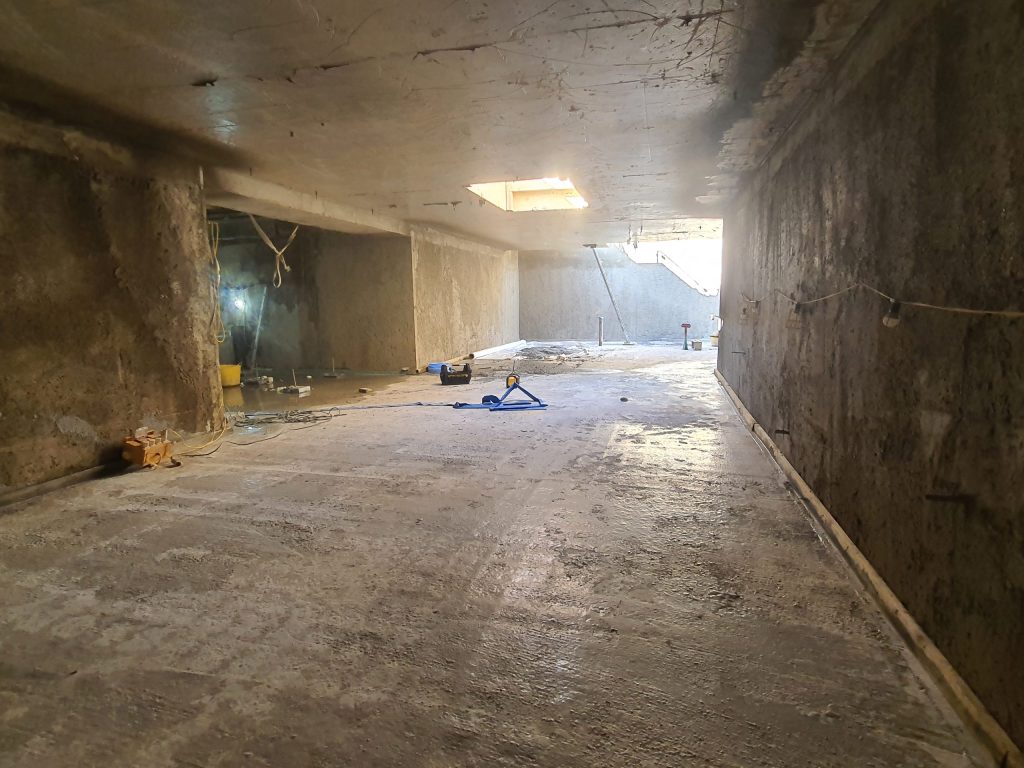
Project Overview
Project Details
Categories: | |
Client: | East Coast Homes Ltd |
Location: | Kislingbury, Northamptonshire |
Surface Area: | 176 square metres |
Completed: | 2021 |
Architect: | PW Architects |
Stage 1 – Retrofit and extension Site preparation, contiguous piles, capping beam & ground floor level
Site preparation
The old carpark and ground of the farmhouse had to be stripped and levelled ready for construction. As the first team on site, Beautiful Basements created access, hard standing and levelled the area for the extension.
Contiguous piles & capping beam
With the area prepared, the heavy machinery could gain access. Contiguous piles (concrete columns linked to each other) were drilled, reinforced, and cast around the perimeter of the new extension basement.
These piles were all then linked with the construction of a reinforced ring beam over the top of each pile and cast as one concrete beam. This ties the top of the columns together, with the bottom much deeper than the excavation will take place. This essentially forms the retaining walls for the crew to work safely within without fear of collapse.
Ground floor slab
The next step was to create the ground floor slab, essentially the ceiling for the new basement. The space was prepared and levelled, reinforced, and cast as one structure, linked to the pile capping beam.
This slab had to be allowed to cure for 28 days before the next stage could begin.
Stage 2 – Creating the Retrofit and extension
With the external ground floor slab cured and self-supporting, the retrofit and extension basements could be created.
Excavating the basements
The internal retrofit basement was created by digging section by section, to a depth of 1.2m. Each metre was excavated, concreted, and packed before the next section was excavated. Once the whole perimeter was excavated the process was repeated, essentially underpinning the underpins.
At the same time the internal works were being carried out, the new extension basement could be excavated. This was excavated in one as the walls and ceiling were already full height and self-supporting. Once excavated and new internal concrete wall was cast to tie all the contiguous piles together.
Casting the floors
With both basements fully excavated and the walls all cast with reinforced concrete, the floor could be created. Steel reinforcing in the walls was connected to the floor reinforcing and the whole footprint of the new basement was cast as one structural slab. This gave the final strength to the building as well as a good waterproof barrier.
Ground floor & steel frame
To complete the build a new structurally integral internal ground floor slab was cast. This was tied into the walls and external ground floor slab, creating one monolithic structure. Internally a steel frame was installed within the basement to give more stability and strength to the old building.
Stage 3 – Retrofit and Extension Waterproofing
The waterproofing regime on this retrofit and extension project had to include a dual-protection system to satisfy the requirements of the warranty provider. Beautiful Basements was the designer of both systems.
Primary System
Type B – Integral protection
All external walls, all concrete slabs (ground and basement floor) were cast with concrete including a waterproof additive. The steel reinforcing within this structure was designed to reduce the cracking to less than 0.3mm, also providing integral protection. All construction and day joints have a crystalising waterproofing slurry applied to them to waterproof natural weak points.
Secondary System
Type C – Drained cavity protection
At the base of all external walls a recessed concrete channel was created within the slab. All walls and the floor were lined with a cavity drainage membrane (CDM). These membranes were linked to two sump chambers via the recessed perimeter channels. Within each sump are two pumps and a high-level alarm. This system is designed to catch any water that is not stopped by the primary system and discharge it automatically. Flushing and maintenance points were installed to allow future servicing of the system.
Both waterproofing systems were designed by Structural Surveyors in Structural Waterproofing (CSSW) in accordance with BS8102:2009
All waterproofing materials were supplied by Triton Systems Ltd
Take a look at some of our similar previous retrofit basement projects. Or click below to contact us and get a quote